




Introducing the innovative Constant Velocity Engine. The future we need now.
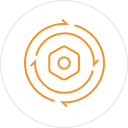
Massive Continuous Torque
Maximum torque for 90% of the stroke vs momentarily for crankshaft engines
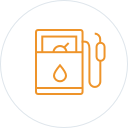
Fuel Efficient
Consumes less than half the fuel to produce the same horsepower
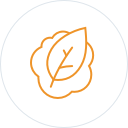
Reduced Emissions
Eliminates 70%+ of exhaust emissions with nearly 100% burn of all fuel
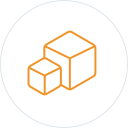
Smaller
Same power in a smaller package permits design & product innovations
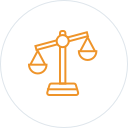
Lighter
Same power with far less weight yields additional fuel savings
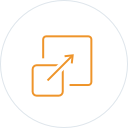
Fully Scalable
Applications from 2 - 20,000+ horsepower Multi-size, multi-fuel, multi-industry, multi-product
Discover Ahiravata's Cutting-Edge Technology
For Two-Wheeler Engines!
Using Constant Torque To Revolutionize Urban Mobility - Modern two-wheeler engines from the Company Ahiravata are made towards revolutionize urban travel by delivering steady thrust all along the way. Our engines guarantee a smooth flow of energy, making every ride powerful as well as smooth, in contrast to traditional engines that only occasionally deliver power. Our technology guarantees continuous performance, overall ride quality, and improving acceleration whether you are speeding through urban traffic or cruising on wide roads.
Excellent Fuel Efficiency for Daily Travel
Our cutting-edge two-wheeler engines are designed towards the method to use the least amount of fuel possible, delivering everyday travelers with substantial savings. Our engines use less gasoline while generating the same amount of power as conventional engines because they optimize fuel combustion. More kilometers per liter, fewer trips to the gas station, as well as less financial strain are all outcomes of this. Because of the increased fuel efficiency & consequently lower carbon emissions, your vehicles are not only economical but also ecologically sustainable.
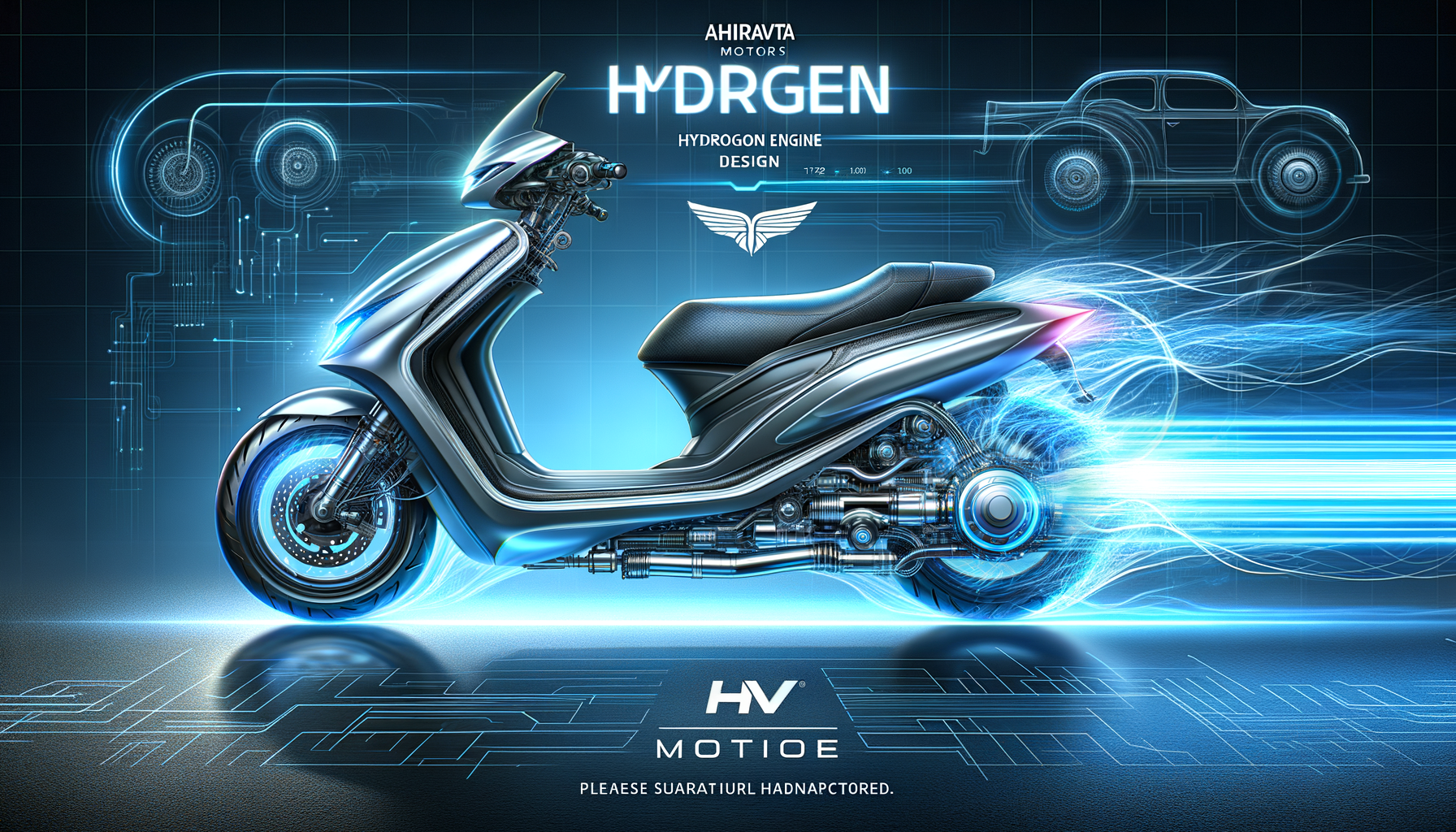
About Ahiravata Motor Corporation Private Limited & CV Global, Inc.
Adopt Low-Emissions Green Riding:
Ahiravata Motor Corporation Private Limited (India) and CV Global, Inc. (USA) are collaborating to bring groundbreaking Constant Velocity (CV) Engine technology to India and other potential markets. This partnership combines cutting-edge innovation with a focus on efficient, high-performance automotive engineering.
Vision for the Future of Internal Combustion Engines:
Ahiravata, a pioneer in advanced engine technologies, aims to revolutionize internal combustion engines for the future. The Constant Velocity (CV) Engine, a product of the strong partnership between Ahiravata Motor Corporation and CV Global, Inc., is set to redefine benchmarks for performance, efficiency, and sustainability across diverse applications.
Adopt Low-Emissions Green Riding:
The design of Ahiravata’s two-wheeler engines places a high priority on sustainability. By assuring that almost all of the fuel is burnt efficiently, our cutting-edge technology significantly lowers exhaust emissions. You can assist yourself in generating a better environment as well as cleaner air by preferring our two-wheelers. Our engines meet the most recent emission regulations, so you can ride sensibly without sacrificing efficiency. Each & every single trip you take contributes to a greener future by decreasing your carbon impact.
Explore Different Types Of Engines
Specifications
Engine Power That Can Be Adapted to Various Riding Experiences
Our two-wheeler engines can effectively handle a wide variety of power related requirements since they are adaptable as well as scalable. Our technology may be modified in order to suit your unique needs, whether you require an engine for the powerful touring motorcycle or a small urban scooter. Our engines can deliver the versatility to accommodate various riding styles & tastes, with horsepower outputs ranging right from modest to high performance levels. This versatility guarantees that Ahiravata.com has an engine solution that delivers the best possible performance & efficiency for any riding requirements.
Generating a Sustainable Future Path
Our goal at Ahiravata is to lead the manner in developing sustainable urban mobility solutions. Our commitment towards lessening our impact on the environment while overall improving the riding experience is showcased by our two-wheeler engines. We wish to revolutionize the two-wheeler market by fusing cutting-edge technology with creative design. Come along with us as we strive for a more hygienic, effective, as well as pleasurable riding experience.
Our Modern engine technology from Ahiravata.com delivers you outstanding performance, remarkable fuel efficiency, as well as a more environmentally friendly ride. With our cutting-edge two-wheeler engines, which are made to make every ride enjoyable, you can now embrace the future of urban mobility. So, let's work together to generate a future that is more efficient as well as sustainable.
Small & Creative Urban Landscape Design
These two-wheeler engines are little yet mighty, built to withstand the rigors of contemporary Metropolitan settings. The lightweight engine made possible by the creative design improves overall mobility as well as makes navigating through crowded city streets & confined places simpler. Manufacturers are also able to generate fashionable as well as nimble two-wheeler models that meet the changing demands of urban riders all thanks to the sleek & tiny form factor. Our technology ensures that performance as well as appearance go hand in hand by encouraging innovation in vehicle design.
Lightweight & Adaptable for Improved Maneuvrability
The two-wheeler engines from Ahiravata.com put an emphasis on control & agility. Our engines' lightweight construction makes handling straightforward, thus enabling riders to handle tight turns & maneuver through heavy traffic with ease. The increased maneuverability improves riding as well as makes both weekend excursions & daily commutes more pleasurable. Longer vehicle life & lower maintenance costs outcome from the engine's decreased weight, which also lessens wear & tear on other parts of the car.
Technology
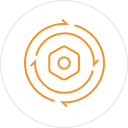
Massive Continuous Torque
The crankshaft mechanism has served a vital role in internal combustion engine design for more than 130 years. However, despite continuous refinement and incremental improvements over time, the crankshaft has reached the end of its useful life.
Crankshaft geometry has inherent design limitations in the transfer of linear force to rotational power. A crankshaft-based engine achieves its peak torque for only one brief moment at close to mid-stroke.
The CVE design achieves its maximum torque starting at 8%* of the stroke after TDC and maintains maximum torque for over 90%* of the stroke after TDC.
Side-by-side static testing of equal displacement crankshaft based versus CVE Technology based designs show that the CVE design boasts a 58%* improvement in torque over today’s crankshaft engine design.
The patented CV Engine/Technology (CVE) replaces the crankshaft completely with a Powershaft and Rodrack Assembly, which fundamentally alters the geometric relationship of the motion of the piston stroke relative to the movement of the rotating shaft. It continuously converts linear reciprocating piston motion to rotary movement and vice versa in the most efficient manner possible.
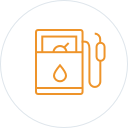
Fuel Efficient
When comparing engine designs producing equal power:
The fuel required by the crankshaft-based engine is far greater because:
- The amount of fuel injected into the cylinder must be substantial enough to last until mid-stroke, where a momentary maximum transfer of linear motion to rotational power occurs
- Due to the asynchronous motion of the opposing pistons, an increased amount of energy is required to propel these pistons through their cycle in order to rotate the crankshaft and drive the other pistons not engaged in the power stroke
- The geometry of the crankshaft to connecting rod to piston connection creates drag and friction due to piston side load on the cylinder walls
- The pistons are not traveling at a constant velocity and are operating at continuously varying speeds throughout the stroke, which creates a pulsation within the crankcase
The fuel required by the CV Engine design is far less because:
- The CVE design requires only a small amount of fuel at the top of the stroke to propel the piston down the cylinder to create continuous maximum transfer of linear motion to rotational power occurs
- The piston and rodrack assembly is one integrated component that is in perfect linear alignment, permitting the pistons to move in synchronous motion, requiring minimal energy to propel the full cycle
- Drag and friction due to piston side load on the cylinder walls is non-existent in the CVE engine design due to perfect linear alignment of the piston and rodrack assembly and the linear bearings that support the travel of the rodrack assembly
- The pistons in the CVE are traveling at a constant velocity and are operating at constant speeds throughout more than 80%* of the stroke, virtually eliminating pulsation within the CVE Powercase
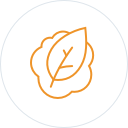
Reduced Emissions & Environmental Impact
When comparing engine designs producing equal power:
Crankshaft Engine Design
- In a four-stroke crankshaft-based engine, the fuel required to obtain optimum performance must be sufficient to sustain combustion until the piston reaches mid- stroke and the fuel charge must simultaneously increase in volume as the volume within the cylinder increases as the piston travels to mid-stroke.
- Due to the required duration of combustion and required piston travel within the cylinder, only half of the stroke remains to eliminate the fuel charge, therefore the entire volume of fuel required cannot be burned by the time the power stroke is complete
- The unburned fuel is therefore wasted and creates additional harmful emissions in the exhaust gasses, which must be captured and processed by the catalytic converter. The use of engine exhaust scrubbing devices such as diesel particulate filters and catalytic converters, which require expensive precious metals such as platinum, palladium and rhodium.
- Due to crankshaft geometry, the piston is subject to side-loading. This side load not only creates friction and drag and negatively impacts torque, the unloaded side of the piston creates a gap between the piston and the cylinder wall, allowing exhaust gases to escape into the crankcase, contaminating the engine oil, requiring frequent and environmentally impactful oil and filter changes.
- According to Lafayette University, almost 30% of all US global warming emissions result from America’s transportation sector. 60% of U.S. transportation emissions come from cars and light trucks, which conveys the significant role vehicle exhaust from internal combustion engines in passenger cars has on our environment and community health.
Read the study…
CV Motion Technology Engine Design
- In the CVE four stroke design, optimum performance is achieved at the top of the stroke, where the volume of the cylinder is relatively small, requiring significantly less fuel to generate the maximum transfer of power
- The maximum transfer of power occurs at close to the top of the stroke in the CV Engine design. This short duration combustion phase allows for nearly the entire stroke to be utilized to complete the total combustion of the smaller required fuel charge by the time the exhaust stroke is initiated
- Due to the absence of the majority of unburned fuel and harmful emissions, the need for a catalytic converter in gasoline engine applications is completely eliminated. The cost savings on a per engine basis is significant. Corresponding reductions in emissions are achieved in diesel engine applications which may permit the elimination of exhaust scrubbing devices such as diesel particulate filters
- In the CVE design, the piston and rodrack assembly functions as one integrated component that is in perfect linear alignment and therefore does not allow the piston to come in contact with the cylinder wall. This eliminates piston to side load. This minimizes drag and friction and eliminates the heat produced by the contact of the piston with the cylinder wall.
- The CVE operates with a fully sealed powercase, much like a sealed transmission case. The lack of piston side loading combined with the sealed powercase prevents combustion by-products from entering the powercase, preventing contamination of the engine oil, virtually eliminating environmentally impactful oil and filter changes.
- The forecasted 70% reduction in exhaust emissions from the use of the CV Engine in all modes of fueled transportation would translate to a reduction from 8,887 grams of CO2 per gallon of gasoline burned to 2,667 grams of CO2 and a reduction from 10,180 grams of CO2 per gallon of diesel burned to 3,054 grams of CO2. The potential impact of the CV Engine on reducing global warming emissions from carbon dioxide is enormous.
Read the study…
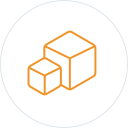
Smaller
To illustrate the significant reductions in physical size that can be achieved via the CVE design, a direct comparison with a comparable crankshaft-based engine follows.
When comparing engine designs producing equal power:
Specifications | Crankshaft Engine Design Subaru FB25 (4cyl, 4 stroke) | CV Motion Technology Engine Design A02 Version (4cyl, 4 stroke) |
---|---|---|
Horsepower | 170 | 193 |
Displacement | 152.4 cu or 2498 cc | 27 cu or 443 cc |
RPM | 5800 (non direct) | 2450 (direct, not geared) |
Height | 23.63″ | 10″ |
Width | 32.67″ | 14.5″ |
Length | 16.93″ | 11.8″ |
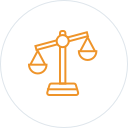
Lighter
The CV Engine design eliminates the crankshaft, the second heaviest component of an internal combustion engine after the engine block.
The CV Engine produces the same power from a much smaller displacement and therefore is lighter overall. The CV Engine also requires fewer total parts in its construction and these parts are generally smaller and lighter as well.
The high compression pressures required in the crankshaft-based design impacts many aspects of the overall engine design, as multiple components must be made robust enough to withstand the very high pressures, which translates to significantly increased engine weight. The CVE design operates at substantially reduced pressures (gas or diesel) which allows for the weight of both the engine and the related subassemblies it would be installed in to be much lighter.
The combined effect of the elimination of the crankshaft, the physically smaller components comprising the engine and the ability to assemble the engine with components of an overall lighter weight construction translates to significant weight savings, on the order of hundreds of pounds even in a modest car size engine.
When comparing engine designs producing equal power:
Specifications | Crankshaft Engine Design Subaru FB25 (4cyl, 4 stroke) | CV Motion Technology Engine Design A02 Version (4cyl, 4 stroke) |
---|---|---|
Horsepower | 170 | 193 |
Displacement | 152.4 cu or 2498 cc | 27 cu or 443 cc |
RPM | 5800 (non direct) | 2450 (direct, not geared) |
Dry Weight | 269 lbs | 71 lbs |
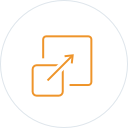
Fully Scalable
The CVE design allows for an extensive range of configurations, several of which are impossible or impractical with a crankshaft-based design. The design of the CVE powershaft allows for unique and highly beneficial designs which creates substantial manufacturing efficiencies, with resultant cost and operational savings.
The tables below highlight some of the applications, configurations and manufacturing benefits.
Configuration | Benefit |
---|---|
Multi-fuel | Gas, diesel, jet fuel, natural gas, hydrogen, compressed air |
Multi-module engine | Combine fueled engine, compressor, air motor (drone) |
Multi-module engine | Combine fueled engine, compressor, air motor (hyper-mileage vehicle) |
Multiple engines | Common, hollow powershaft allows for multiple, redundant engines |
Multiple engines | Coupled engines brought on/off line (more power vs. fuel savings) |
General aviation | Redundant engines; lightweight diesel application, diesel fuel vs. avgas |
Automobile | Compact, mid-engine designs without sacrificing interior space |
Range extender (battery) | Small engine recharges batteries for electric motor without stopping |
Range extender (no battery) | Small engine powers DC generator to directly power electric motors |
Recreational vehicles | Reduced emissions create acceptance in environmentally sensitive areas |
Generators / Heavy equipment | Greatly reduced fuel use creates less downtime & cost savings |
Ocean freight / Cruise Ships | Multiple engines coupled for high speed, “green” ocean crossings |
Ocean freight / Cruise Ships | Uncouple all but one engine for low emission in-harbor operation |
Ocean freight / Cruise Ships | Massive fuel savings from propulsion engines and ship’s electric generators |
Trucking industry | Massive fuel savings for fleet operators |
Trucking industry | Fuel savings mean the difference between profit & loss for owner/operators |
Marine industry | Same power from smaller engine creates more useable space |
Marine industry | Same power with less weight improves performance and saves fuel |
Scalable size | Same horsepower produced with smaller displacement |
Scalable output | Same displacement generating greater horsepower |
Manufacturing | Benefit |
---|---|
Common platform | Many engine variants (4, 6, 8 cylinders) from two CV engine configurations) |
Hollow Powershaft | Engage or disengage multiple engines to save fuel or provide power |
Hollow Powershaft | Reduces number of engine variants required; less parts inventory |
Simplified production | Reduce the number of engine variant production lines; faster production |
Less factory space required | Reduced factory overhead and building maintenance expenses |
Less personnel required | Reduced payroll and benefits expenses |
Reduced number of tools | Production line elimination also eliminates tools required |
Reduced number of parts | Reduced parts manufacturing, storage and inventory tracking expense |
Reduced number of suppliers | Simplified supply chain; less dependency on suppliers; reduced delays |
Smaller engine dimensions | More storage in same space; more engines shipped in same container |
Vehicles | Benefit |
---|---|
Lighter sub-assemblies | A significantly lighter engine allows for substantially lighter sub-assemblies |
Smaller braking components | Less mass due to reduced component weight allows for smaller brakes |
Reduced overall weight | Weight savings from engine & all sub-assemblies adds to fuel savings |
Reduced fuel consumption | Combined effect from engine operation, lighter engine and components |
Smaller, simpler transmissions | Low RPM, high torque engine permits 2 forward, 1 reverse gearing |
Lower center of gravity | Horizontally opposed engine, smaller dimensions, mid-engine applications |
Storage & passenger space | Reduced engine volume opens up space for people and cargo |
Trucking industry | Reduced overall weight permits heavier payloads |
Simpler to maintain | Sealed power case equate to elimination of oil changes; less waste |